The current heat wave engulfing the U.S presents big problems for all our employees. Particularly at risk are those who work in high air temperatures and/or high humidity, near radiant heat sources, and/or engage in strenuous physical activities. In other words, conditions typically found on the turbine deck.
When a person works in a hot environment, the body must get rid of excess heat to maintain a stable internal temperature. We do this mainly through circulating blood to the skin and through sweating. Cooling the body becomes more difficult when the air temperature is close to or warmer than normal body temperature. Blood circulated to the skin cannot lose its heat and sweating becomes the main way the body cools off. But sweating is ineffective in high humidity because the sweat can’t evaporate. In extremely low humidity, sweat may instantly evaporate from the skin, disguising the need to replace that vital water.
If the body cannot get rid of excess heat, the core temperature rises and the heart rate increases. Loss of salts (electrolytes) can impair muscle and brain function. Injury can also result from sweaty palms, fogged-up safety glasses, dizziness, loss of concentration, and burns from hot surfaces or steam.
Excessive heat can cause a range of illnesses, from heat rash and heat cramps to heat exhaustion and heat stroke. Initially, the person begins to lose concentration and has difficulty focusing on a task. He may become irritable or sick, and often loses the desire to drink. The next stage is most often dizziness or even fainting. Heat stroke can result in death and requires immediate medical attention.
The best way to prevent heat-related illness is to make the work environment cooler by staying in the shade and employing fans and adequate ventilation, or even air conditioning. If it is still hot, employ safe work practices such as enforced work/rest cycles, water breaks, and providing an opportunity for workers to build up a level of tolerance to working in the heat. Be sure to include these prevention steps in worksite training and plans. Remember to refrain from alcohol intake the night prior and coffee during the shift. Alcohol, coffee and some prescription medications are diuretics which increase the rate of fluid loss. If the temperature is soaring and you are not urinating, you are not getting enough fluids.
It’s important to know and look out for the symptoms of heat-related illness in yourself and others. Plan for an emergency and know what to do – acting quickly can save lives!
High Bearing Loading
/in Steam Turbine Tips /by Mike.LakePast Turbine Tips have covered the main reasons for bearings to wipe: 1) Insufficient lube oil supply, 2) Low lube oil pressure, and 3) Water in the lube oil. Every once in a while a fourth cause appears: High bearing loading.
Proper bearing loading is calculated by the elevations of the bearings, component weights and shaft alignments (bending moments, lateral, torsional). The OEM calculates the elevations and coupling alignments during the design process, based on the catenary curve (or sag chart). Calculations ofbearing loadings and alignment are usually accurate based on the design engineers’ mathematical calculations and computer model for the rotor’s geometry, speed, weight, and bearing design.
The Catenary Curve
Most of the time, high bearing loading is caused by misalignment of the turbine power train from the original design. That is, some force has moved the components from their original alignments. The source of the bearing failure can be eliminated by carefully measuring and re-aligning to the original specifications. But we have seen examples where the original calculations either were not accurate orover years of operation the bearing pedestals had moved.
Recalculating bearing loading is an arduous and potentially expensive process, so all other contributing factors should be eliminated before attempting this course. If necessary, TGM can perform the recalculation and re-alignment without the participation of the OEM. On three bearing units, it is not uncommon to utilize a dynamometer to check bearing loading during alignment and their adjustments.
An Attitude of Safety
/in Safety Tips /by Mike.LakeHave you ever noticed that people who are successful in life, or are just happy, tend to have a positive attitude? And so it is with safety. Look at it this way–safety rules and procedures are written to protect you from harm. They are not written to make your work life more uncomfortable or inconvenient. After all, safety equipment and training costs your employer additional upfront money.
If you cooperate in safety matters, not only is there a lesser likelihood of you getting hurt, but you will not be doing battle with the people enforcing the safety rules. In addition, you should feel more confident on the job knowing you have a better chance of making it thorough the day without injury. Less fear of injury and the thought of no one on your back has to brighten your day!
We are not perfect. Even the best of us can forget or make errors in judgment. To maximize our safety efforts, we must look out for one another. If someone tells you that you are not working in a safe manner, do not become angry or defensive. They are just looking out for your well-being. If you did not know you were doing something wrong, be thankful your errors were noted before someone got hurt. If you simply forgot or got a little careless, be grateful that someone cares enough to get you back on track. If you see someone doing something unsafe, speak up, but do so diplomatically. Treat others just as you would like to be treated in the same situation.
Remember, attitude affects behavior. If you have a positive attitude, odds are you will exhibit safe behavior. A negative attitude toward safety will only cause conflict, stress and, ultimately, an accident.
This month, TGM celebrates over two calendar years without an OSHA-recordable accident. Please join us in our goal of an accident-free year.
Prevent Bearing Failures
/in Steam Turbine Tips /by Mike.LakeTGM believes that forced outages can be avoided with proper maintenance and periodic assessments performed during a short outage. Unfortunately, we see all too many examples of too few inspections and too little maintenance.
Here’s an example from one of our recent projects. The picture below is a gearbox bearing on a line shaft gearbox that had not been inspected for several years. One bearing is on one side of the bull gear and there is another just like it on the other side. As you can see, the bearing is fully wiped – it is a wonder it is still functioning. If the bearing had failed, the entire gear set would have collapsed, necessitating a compete replacement. The gear set is expensive but the real loss would be the substantial downtime for the plant as a new gear set is manufactured.
An investigation of the cause revealed very dirty oil and water in the oil but the root cause was alignment issues. We found improper spacing between the drive shaft couplings which put stress on this combination thrust and radial bearing. The increased heat from this stress led to oil degradation, made worse by the water contamination. Consequently, poor lubrication caused the bearing to wipe. Alignment issues can also be detected through vibration changes or abnormal wear patterns on the complete set of bearings. These “running assessments” are crucial to predicting problems before they cause serious damage.
It is relatively inexpensive to inspect the bearings every two years and damaged bearings can usually be replaced during the outage window. However, an incident such as overheating, abnormal vibration, or water ingress is evidence of potentially serious problems and must be addressed immediately. Any extra effort required to keep the oil clean and relatively water-free will also signal the need for an early inspection/overhaul. (See also our past Turbine Tips for maintaining the Lube Oil system and also note that re-Babbitted bearings should be UT inspected for proper bonding of the Babbitt to the shell.)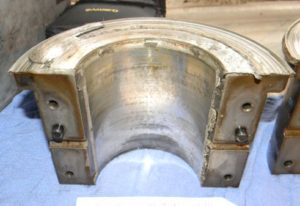
Big Problem = Hot! Hot! Hot!
/in Safety Tips /by Mike.LakeThe current heat wave engulfing the U.S presents big problems for all our employees. Particularly at risk are those who work in high air temperatures and/or high humidity, near radiant heat sources, and/or engage in strenuous physical activities. In other words, conditions typically found on the turbine deck.
When a person works in a hot environment, the body must get rid of excess heat to maintain a stable internal temperature. We do this mainly through circulating blood to the skin and through sweating. Cooling the body becomes more difficult when the air temperature is close to or warmer than normal body temperature. Blood circulated to the skin cannot lose its heat and sweating becomes the main way the body cools off. But sweating is ineffective in high humidity because the sweat can’t evaporate. In extremely low humidity, sweat may instantly evaporate from the skin, disguising the need to replace that vital water.
If the body cannot get rid of excess heat, the core temperature rises and the heart rate increases. Loss of salts (electrolytes) can impair muscle and brain function. Injury can also result from sweaty palms, fogged-up safety glasses, dizziness, loss of concentration, and burns from hot surfaces or steam.
Excessive heat can cause a range of illnesses, from heat rash and heat cramps to heat exhaustion and heat stroke. Initially, the person begins to lose concentration and has difficulty focusing on a task. He may become irritable or sick, and often loses the desire to drink. The next stage is most often dizziness or even fainting. Heat stroke can result in death and requires immediate medical attention.
The best way to prevent heat-related illness is to make the work environment cooler by staying in the shade and employing fans and adequate ventilation, or even air conditioning. If it is still hot, employ safe work practices such as enforced work/rest cycles, water breaks, and providing an opportunity for workers to build up a level of tolerance to working in the heat. Be sure to include these prevention steps in worksite training and plans. Remember to refrain from alcohol intake the night prior and coffee during the shift. Alcohol, coffee and some prescription medications are diuretics which increase the rate of fluid loss. If the temperature is soaring and you are not urinating, you are not getting enough fluids.
It’s important to know and look out for the symptoms of heat-related illness in yourself and others. Plan for an emergency and know what to do – acting quickly can save lives!
Beware Exploding Sockets
/in Safety Tips /by Mike.LakeHytorc® bolting heads have long been regarded as a safer alternative to hammering on a striking wrench to remove stubborn case bolts. But even impact sockets can shatter under extreme Hytorc® pressures, sending shrapnel rocketing across the turbine deck. These explosive failures can cause serious injury or even death.
These failures can be reduced, but not eliminated, by using the correct socket. Impact rated sockets must be used at a minimum. Old or worn sockets are of particular concern. Ill-fitting sockets do not fit tight on bolt heads. This changes the stress points from the corners to the flats of the sockets and causes them to fail. Best practice is to inspect sockets regularly and color code or otherwise identify them for this use. Another check for reliability would be to have the sockets inspected for potential indications of stress using NDE methods. Hytorc® makes their own sockets and this may give an extra level of confidence. However, in their safety note, Hytorc® only prohibits the use of altered, heavily used, damaged or chrome sockets.
Any socket can fail, so take steps to mitigate the result. If possible, shroud the socket with a piece of pipe cut slightly bigger than the diameter of the socket and same height. If the socket fails, the pipe will hold everything inside. TGM is currently investigating a fiber impregnated tape designed to contain the debris. We also recommend tying off the head to prevent it dropping or flying off after a failure.
Be aware of your hydraulic forces. Sockets are prone to failure when torqued more than twice the specified amount for assembly. Backup wrenches may not be rated for the torque applied. Limit torque to the capacity of the weakest tool in the application. Hytorc® publishes charts on their website which convert pump pressure to torque applied for each of their tools.
Finally, protect your personnel. No one is to be in contact with the head or backup wrenches after initial clamping pressure is applied and until pressure is released. Determine the potential debris path and keep personnel away from the area. You can also use a piece of plywood or metal as a shield. Face shielding is recommended as PPE for all personnel near the danger zone.
Remember that Hytorc® equipment is dangerous and must only be operated by trained individuals. Best practice is to have the same person operate both the tool head and the pump. When this is not possible, the pump operator must be in sight of the tool operator. Three way communication must be used between them.
Loss of Lube Oil (Emergency Lube Oil Systems)
/in Steam Turbine Tips /by Mike.LakeWeekly maintenance checks on emergency lube oil systems should include verifying the adequacy of any battery backup system and testing the pressure switches and controllers that activate backup pumps. These tests should be performed to ensure the backup systems are fully functional should a loss of power or lube oil event occur. These simple efforts of prevention are inexpensive compared to the expenditures related to a turbine coming down without sufficient lube oil.
Safety Tips
/in Safety Tips /by Mike.LakeZero OSHA Recordable Accidents for 528th Consecutive days!
Safety is Turbine Generator Maintenance’s top priority. TGM puts safety above all other considerations and expects that devotion from every TGM employee. Please see our dedicated Safety section of our website for more information on TGM’s Safety Program.
COMMON SENSE AND ACCIDENT PREVENTION
The experts say at least 80% of industrial accidents are caused by unsafe acts on the part of employees–and not by unsafe conditions. Here are a few actions, paired with safety suggestions:
Awareness of your environment, self-preservation, and concern for your fellow workers are all factors in good common sense. All workers can prevent themselves from getting hurt.