Free and emulsified water are the two most harmful conditions in a lubricating system. The incompressibility of water overrides the hydrodynamic oil film that protects bearings, leading to excessive wear. As little as one percent water in oil can reduce the life expectancy of a journal bearing by as much as 90 percent.
Water will also degrade the life of your lubricant. Moisture contamination can promote the oxidation of the oil by up to 10 times, breaking down the hydrocarbon chains and decreasing the lubricating properties.
Oils containing some types of additives are even more vulnerable to water contamination. Sulfurous AW and EP type additives and phenolic antioxidants are readily broken down by water. This not only destroys their usefulness, but the destruction forms acids which can corrode soft metals such as Babbitt, bronze and brass. The copper, lead, and tin released from this corrosion are catalytic metals which actually accelerate the process. Even synthetic oils containing dibase esters and phosphate esters are not immune. These compounds are known to react with water and form acids, increasing corrosion and degrading the base stock.
Water can disperse other additives such as demulsifying agents, detergents and rust inhibitors, resulting in sludge and sediment buildup, filter plugging and poor oil/water demulsibility.
There is no safe level of water contamination. While maintaining contamination below the saturation point will reduce the levels of free and emulisified water, any amount will start the cycle of degradation.
We recommend that you send a lube oil sample out for analysis on a monthly basis. Then read their report very carefully, noting all metals and water contamination. The service should also provide a narrative of the findings. If you need any help in interpreting the report, please contact us at Ask Mr. Turbine.
Click Here to ask your own question of TGM’s Mr. Turbine or call the 24 Hour Hotline at 888.MrTurbine (888.678.8724)
69th Annual AREGC Conference
/in Events /by Mike.LakeWe are at the 69th Annual AREGC Conference in Lanier Islands, Georgia this week. Please stop by and visit us if you are attending. This year’s conference is being hosted by Oglethorpe Power Corporation. Thank you to all those who organized the event!
New 1st Stage Bucket Installation
/in Events /by Mike.LakePSG’s Steam Path Repair Facility, located just outside of St. Louis, Missouri, has been busy this spring. One of the many projects we executed last month was the installation of new 1st stage buckets on an industrial GE Steam Turbine. The time and precision it takes to successfully install these buckets is extremely impressive. The meticulous attention to detail by our trained technicians allowed us to complete the installation safely, on-time, and with the highest level of quality. Great work team!
2018 Frame 6 User’s Group Conference
/in Events, News /by Mike.LakeWe look forward to seeing everyone at this year’s Frame 6 Users Group Conference in Ponte Vedra Beach, Florida! It should be another fun event. Please stop by Power Services Group at Booth #13 during the Vendor Trade Show. Safe travels and see you next week!
CPS Energy tees off United Way campaign to support SAMMinistries
/in Events /by Mike.LakeGreat work by everyone that made this possible. PSG is proud to have been part of this event and the good that it has done for the San Antonio community. The volunteers that make all of this happen are amazing individuals, thank you!
PSG is equipped and ready to tackle your Journal and Shaft Machining Projects
/in News /by Mike.LakePower Services Group’s field machining division, Orbital Energy Services, has successfully repaired thousands of shafts and bearing journals in power and industrial facilities across the globe over the past 20 years. Our unique, on-site machining process requires absolutely no need for shaft rotation, and avoids the issues related to removing and shipping equipment to a shop: costly mobilizations, exorbitant shipping costs, potential damage during shipment, valuable lay down space, and plant crane and rigging requirements. Orbital Energy Services’ finely tuned and safe processes coupled with a full range of equipment ensure customers receive the highest quality at a competitive price. If you have a journal or shaft machining project, planned or an emergency, please contact us anytime for a fast response.
The Ugly Effects of Water in Lube Oil
/in Steam Turbine Tips /by Mike.LakeWater will also degrade the life of your lubricant. Moisture contamination can promote the oxidation of the oil by up to 10 times, breaking down the hydrocarbon chains and decreasing the lubricating properties.
Oils containing some types of additives are even more vulnerable to water contamination. Sulfurous AW and EP type additives and phenolic antioxidants are readily broken down by water. This not only destroys their usefulness, but the destruction forms acids which can corrode soft metals such as Babbitt, bronze and brass. The copper, lead, and tin released from this corrosion are catalytic metals which actually accelerate the process. Even synthetic oils containing dibase esters and phosphate esters are not immune. These compounds are known to react with water and form acids, increasing corrosion and degrading the base stock.
Water can disperse other additives such as demulsifying agents, detergents and rust inhibitors, resulting in sludge and sediment buildup, filter plugging and poor oil/water demulsibility.
There is no safe level of water contamination. While maintaining contamination below the saturation point will reduce the levels of free and emulisified water, any amount will start the cycle of degradation.
We recommend that you send a lube oil sample out for analysis on a monthly basis. Then read their report very carefully, noting all metals and water contamination. The service should also provide a narrative of the findings. If you need any help in interpreting the report, please contact us at Ask Mr. Turbine.
Click Here to ask your own question of TGM’s Mr. Turbine or call the 24 Hour Hotline at 888.MrTurbine (888.678.8724)
2018 NAES O&M Conference
/in Events /by Mike.LakeWe look forward to seeing everyone at this year’s NAES O&M Conference in Colorado Springs, Colorado! It should be another fun event. Please stop by the Power Services Group booth during the Vendor Trade Show. Mike Lake and Gary Beck will be in attendance representing PSG and will be looking forward to meeting everyone. Safe Travels and see you next week!
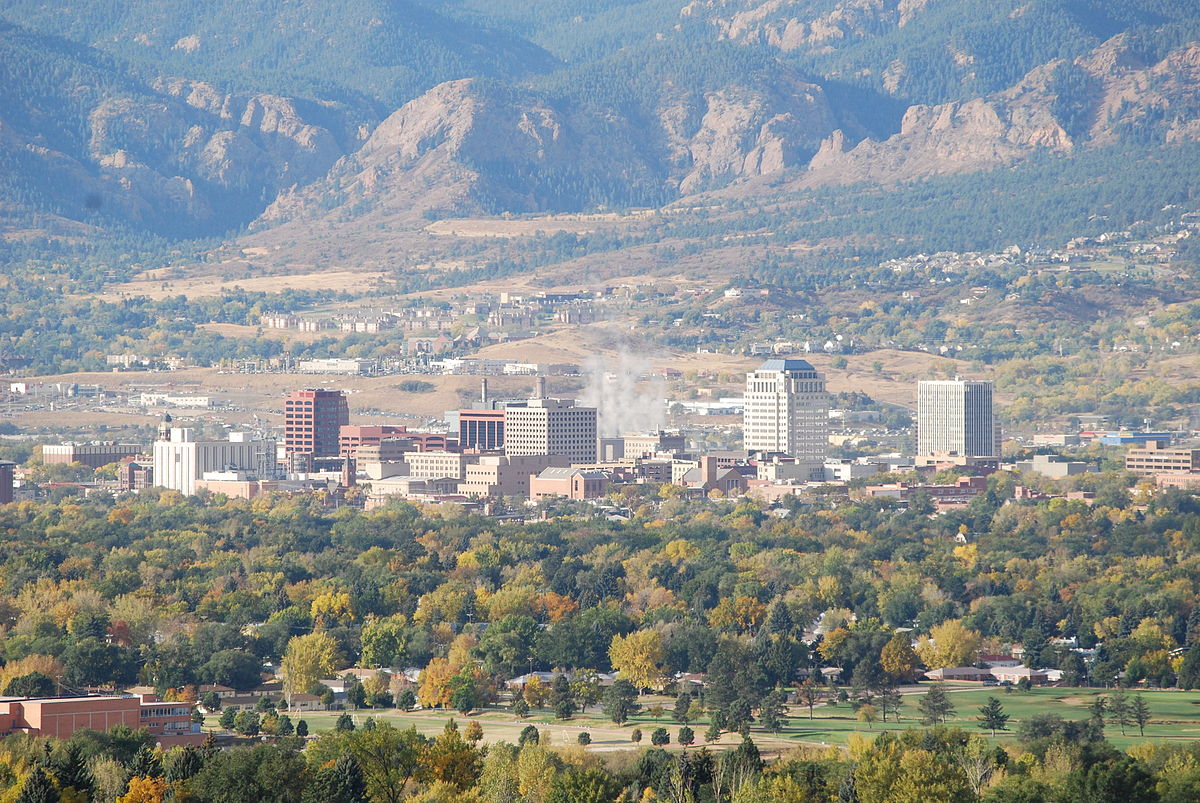
Rotor Axial Position Sensor
/in Controls Tips /by Mike.LakeThis disaster can averted by monitoring and understanding the Rotor Axial Positioning sensor. The probes of this sensor are positioned towards the collar so that the axial movement of the shaft in the direction of the generator (the usual direction of rotor thrust) will cause the gap between the probes and collar to increase. If this gap increases, it is an accurate indication that the thrust bearing Babbitt has been compromised and that the rotor is not in its proper axial position. Your I&E Engineer can determine the maximum fail-safe gap based on the minimum measured axial wheel clearance and the total thrust bearing float measurements from the last inspection (if available).
The squeal that you heard just before the machine crashed came from a “squealer ring”, which is sometimes found on older units. Similar to the fins at the end of your car’s brake pad, the ring will emit an unmistakable loud pitch sound when the machine has reached the limit of its axial thrust. If you hear this sound, immediately manually trip the unit and give us a call. Your unit is in immediate need of a major overhaul.
The axial position probes used in this modern supervisory application are proximity probes, very similar to that used in vibration systems. These probes do not contact the collar. The distance (the gap) between the collar and the probe tip is determined by the use of a high frequency magnetic field. As the rotor moves axially, the gap changes and the output signal varies proportionally. The probe tip is adjustable within the bracket assembly for an initial gap setting using a feeler gauge. This mechanical gap setting should be set by the recommended drawing specifications. However, the preferred method is to make final corrections electronically. These probes are usually set to -8.0 volts +/- 1 volt.
Some older machines use thrust trip devices that use oil pressure through a set of nozzles to a collar. These trip devices have been proven to be very reliable. This oil pressure provides a warning should the thrust bearing babbitted pads wear down to a predetermined amount. Further wear will cause the unit to trip due to the high increase in pressure. This trip takes place so that serious damage does not occur to other turbine parts.
GEUS Major Inspection Video Customer Insight
/in Videos /by Mike.LakeSteam Turbine Major Inspection LONG
/in Videos /by Mike.Lake