2021 American Nuclear Society Conference
/in News /by Mike.Lake
We had an excellent time at the 2021 American Nuclear Society conference in Marco Island, Florida. It was great to meet with some of our existing customers, as well as introduce our services to prospective new customers. We hope everyone enjoyed the event and has a safe trip home. See everyone next year!
Join us at the 2021 American Nuclear Society Conference in Marco Island. The exhibit hall is open and we’re ready to discuss how we can help with your nuclear steam turbine services. pic.twitter.com/5ZKEiv2knk
— Mr. Turbine (@MrTurbinePSG) August 10, 2021
Steam Turbine Inspection & Repair Services
/in News, Steam Turbine Tips /by Mike.LakeTurn-Key Inspections
Power Services Group (PSG) has the ability to provide full turnkey inspections on steam turbine generators for most OEM manufacturers. PSG provides total turnkey outage performance including technical direction, engineering, project management & coordination, supervision, labor, tooling, repairs, parts sourcing and/or manufacturing, and start-up support. We support fossil and nuclear steam turbines ranging from 1MW to 1,300MW for all major OEMs. We service all industry types including, but not limited to: industrial, paper/pulp, marine, steel/aluminum, chemical and petrochemical, utility, nuclear, and independent power producers.
Contact Us today to learn how we can help you with your next steam turbine project.
Services Provided: | Common Repair Services: |
|
|
July Safety Update
/in News, Safety Tips /by Mike.LakeWe’ve completed the month of July with zero OSHA-recordable injuries and have a TRIR of 0.00 for the year. We continue to be proactive in identifying potential hazards and maintaining our safety-first mindset. Great job by our HSE Director, Shannon Scruggs, our Repair Facility Management and Technicians, and each one of our Field Service Project Management teams for engraining our safety culture throughout the organization. Nice job everybody!
American Nuclear Society Conference
/in News /by Mike.Lake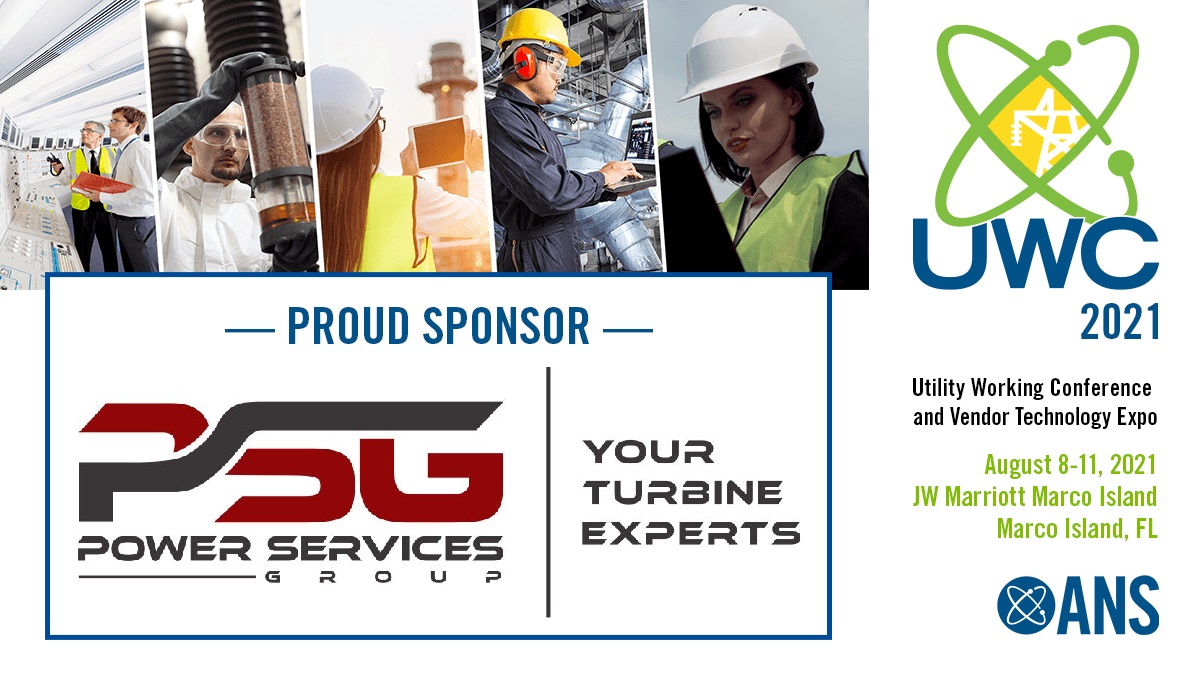
Westinghouse Steam Turbine Major Inspection
/in News, Project Spotlight, Steam Turbine Tips /by Mike.LakePower Services Group, Inc. (PSG) was contracted to perform a major inspection on an industrial Westinghouse steam turbine generator at a paper mill in the Midwest United States. PSG arrived and began mobilization activities. The office and tool containers were off-loaded and the turbine deck set up for the outage. The set-up personnel were safety orientated for the customer’s specific safety policy before work commenced. During the project, a Safety Meeting was held prior to the start of any work. The Safety Meeting topics were based on work activities to be performed during the upcoming shift. In addition, hazardous observations which could impact the safety of the team were discussed and resolved. Prior to performing work, a Job Safety Analysis (JSA) form was completed by the work team. This project had zero accidents and zero first aid incidents.
The unit was taken offline and allowed to cool down over the weekend. The outage began after Lockout / tag out (LOTO) was accomplished. The instrumentation was removed by plant E&I personnel. The V-1 and V-2 control valves were removed from the turbine casing and put on stands. The valves were disassembled and inspected and NDE was performed on the poppets and valve stems. The casing bolts and dowels were removed from the HP and LP turbine casing. An “as found” swing check was performed. The coupling TIR was recorded. The coupling bolts were removed, and the coupling separated. A 4-point face reading was recorded during disassembly. The casing was rigged and jacked up, using jack bolts, about two inches and leveled before total removal. The casing was removed and flipped to access the upper half diaphragms for removal. The thrust bearing clearance was checked before disassembly. A set of wheels and packing clearances were taken with the rotor in running position. The thrust bearing was disassembled, and the total float and strike points were recorded. A set of oil bore measurements were taken before removal of the turbine rotor.
The rotor was removed and prepped for blast cleaning and staged on the turbine deck. The upper half and lower half diaphragms were removed and staged on pallets for blast cleaning. The rotor and diaphragms were blast cleaned and NDE inspected. The axial and side slips were recorded and found to be in tolerance.
The generator field was removed from the generator stator for inspection. The electrical inspection of the generator was performed by a plant subcontractor. Some minor cleaning was performed on the stator and rotor. The generator coolers were disassembled, cleaned and vacuum tested; with no leaks found. The coolers were reassembled with new gaskets and tested before startup.
The turbine and generator bearings were cleaned and dimensionally inspected. The bearings were UT’d to check for bonding issues with the base metal. The #2 journal bearing failed NDE. A new bearing was supplied by the customer and was installed. The turbine and generator oil seals were cleaned and dimensionally inspected. The #3 inboard oil seal had excessive clearance. The oil seal was sent out for repair and final machining.
The control valves were disassembled, cleaned and inspected. The valves were blue checked upon reassembly. The trip throttle valve was disassembled, cleaned and inspected. It was blue checked during reassembly to verify proper contact. The spray chamber was disassembled, cleaned, and inspected. The lube oil pumps were removed from the lube oil reservoir for inspection. The pumps were disassembled, cleaned, and inspected. PSG rebuilt the steam driven lube oil pump. The lube oil tank was cleaned by a plant subcontractor. The lube oil coolers were disassembled, cleaned and vacuum tested with no leaks noted. The lube oil system was flushed for 24 hrs. using the existing pumps.
The unit was brought up and over speed tests were performed. The mechanical tripped at 3970 rpms. The electrical tripped at 3792 rpms. The unit was put online and brought up to partial load. PSG was released from the customer’s site.
2021 Customer Satisfaction
/in News /by Mike.LakeOur Customer Satisfaction Survey results are in, and we are happy to share that we received a 93.3% overall score for projects completed in the 1st half of 2021. We take pride in our work, and strive to complete every project to the complete satisfaction of our customers. This score is a testament to our focus on customer satisfaction, and at the same time provides us with opportunity for improvement. We strive to help our customers achieve their goals, and look forward to continuing to be the service provider of choice for companies with power generating equipment across the globe.
Still considering performing a turbine outage this Fall or next Spring?
/in News, Steam Turbine Tips /by Mike.LakeRegardless of whether or not your steam turbine is cycling or base load, it may be difficult to pinpoint when the next maintenance inspection should be performed. We have a solution to help you determine when to schedule your next steam turbine inspection – providing peace of mind that you are scheduling your maintenance outages when they are needed, not spending money too soon, and not waiting until its too late.
A Running Condition Assessment may provide you (or your insurance company) with the peace of mind that the unit is not nearing a failure point, and can continue to operate. Alternatively, the Running Condition Assessment may tell you that an immediate outage should be scheduled to avoid a component failure. The Running Condition Assessment can provide you with the information needed to properly schedule your next steam turbine outage.
- A Running Condition Assessment allows us to assess the health of your turbine generator while the unit is in operation – no need to bring the unit offline.
- This assessment typically includes one specialized technician and equipment at your facility for 3 – 5 days, minimizing the people and time on-site.
- After completion of the Running Condition Assessment you will receive a detailed report on the current condition of your turbine, providing you with vital information for future decision-making.
- The cost of a Running Condition Assessment is negligible compared to the cost of a turbine outage.
To learn more about our Running Condition Assessment program, CLICK HERE.
To request a quote and check availability for a Running Condition Assessment, CLICK HERE.
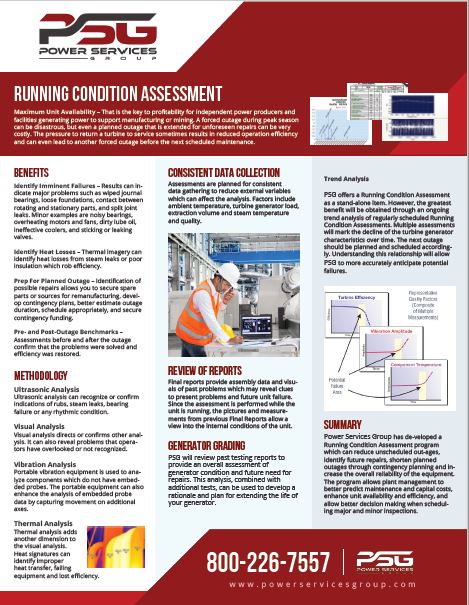
4 Years since last Lost Time Injury
/in News, Safety Tips /by Mike.LakeWe have surpassed the 4-year mark since our last Lost Time Injury! This is a tremendous accomplishment by everyone on the PSG Team.
This accomplishment can be attributed to our proactive safety-first mindset in identifying potential hazards for every task we undertake. This is all made possible by the great people we have at PSG – our HSE Director, Shannon Scruggs, our Repair Facility Management and Technicians, and each one of our Field Service Project Management teams for engraining our safety culture throughout the organization. Fantastic job everybody!
Combustion Turbine Inspection Services
/in Combustion Turbine Tips, News /by Mike.LakePower Services Group (PSG) executes combustion inspections, hot gas path inspections, and major inspections on combustion turbine generators all over the World. PSG provides total turnkey outage performance including technical direction, project management, coordination, supervision, labor, tooling, and start-up support. We provide combustion turbine services on the following unit types:
OEM | Combustion Turbine Type |
General Electric | Frame 3, 5, 6, 6B, 7, 7B, 7E, 7EA |
Westinghouse | 251AA, 251B, 301G |
Alstom | GT8, GT11 |
Contact Us today to learn how we can help you with your next combustion turbine inspection.
Services at a Glance
Ready to Serve Your Needs
Power Services Group brings you a wide range of services specific to industries like yours, offering exceptional value and responsiveness. We can hit the ground running and deliver results so you can have peace of mind and your equipment is always available.
Contact Us Today
125 SW 3rd Place, Suite 300
Cape Coral, FL 33991
Phone: (800) 226-7557