Emergent Steam Turbine Valve Components Need for your Spring Outage?
Contact us today to learn how we can provide you with high quality/low cost valve components for your Steam Turbine. We manufacture a variety of valve components for various Steam Turbine OEM types for the fossil and nuclear industries.
If your outage is here and an unexpected need arises we can reverse engineer and manufacture components through the simple process outlined below.
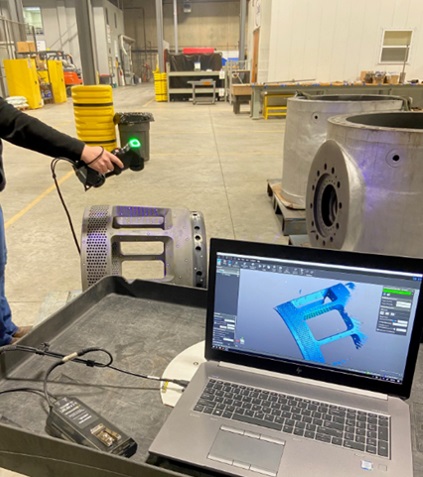
- Sample Received– Whether it’s a stock item or an item made to order for a special application, the process begins with a new or used sample.
- Reverse Engineering – After receiving your sample, we confirm all required properties using our state of the art equipment; properties such as dimensions, hardness, and material composition.
- Design – From the reverse engineering data, a detailed CAD manufacturing drawing is created in accordance with international design standards.
- Price Estimate – A price estimate is provided to the customer for the finished part. Typically, savings are in the range of 15-30% under standard retail pricing. More savings can be realized as production quantities increase.
- Manufacture – Upon agreement on the design and price, we manufactures the part, keeping you updated on status along the way. After passing a stringent quality inspection, parts will ship immediately.
This entire process can be expedited to get your turbine back online as quickly as possible. We hope to hear from you the next time you need any steam turbine valve components.
![]() |
![]() |
![]() |
![]() |
![]() |
![]() |